Virtuelle Werkzeugmaschine
Verbesserung der Energieeffizienz
Das Simulationsmodell
Ständig steigende Anforderungen an die Produktivität und Effizienz von Werkzeugmaschinen erfordern eine entwicklungsbegleitende Verifikation der Steuerungs-Applikationssoftware und Ansätze zur Energie- und Ressourcenschonung ab dem ersten Tag des Produktlebenszykluses.
Das Benefiz besteht in der Prüfung von Betriebssicherheit und Zuverlässigkeit des aus Steuerung und Anlage bestehenden Gesamtsystems bereits vor der Inbetriebnahme. Die Realisierung geschieht in der Entwicklung eines Simulationsmodells der Werkzeugmaschine. Anschließend wird das Modell an eine reale Steuerung zur „Hardware-In-the-Loop-Simulation“ gekoppelt.
Die Energiemessung
Für die Energieeffizienzuntersuchungen von alten und neuen Maschinen werden im Vorfeld Energiemessungen mit dem Messequipment FLUKE 434 II an der realen Werkzeugmaschine vorgenommen. Die gewonnenen Messergebnisse werden mittels geräteabhängiger Software über eine USB-Schnittstelle ausgelesen und stehen in üblichen Weiterverarbeitungsformaten zur Verfügung.
Validation und Ermittlung der Energieeffizienz
Bereits damit können Aussagen über die verbrauchsrelevanten Komponenten getroffen werden. Der Abgleich des Simulationsmodells mit den realen Energieströmen dient der Validation des Modells. Als Resultat steht die Ableitung rentabler Energieeffizienzmaßnahmen auf Basis des entwickelten Simulationsmodells. Entsprechende Ergebnisse aus dem Bereich des Werkzeugmaschinenbaus weisen Einsparpotentiale von bis zu 50 Prozent auf, bezogen auf eine konkrete Fertigungsaufgabe. Ohne Weiteres kann dieses Prinzip auf andere Werkzeugmaschinen übertragen werden. Hierbei gibt es keine Einschränkungen hinsichtlich der Anschlussleistung der Maschine.
Projekterfahrungen
Branchen: Maschinenbau, Energietechnik, Umwelt und Verkehr
Referenzen: Forschungsprojekte Industrielle Messtechnik
Ihr Ansprechpartner
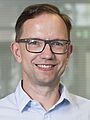