October 2021 | Vibration sensors transmit real-time analysis data via RF technology for vibration diagnostics of the rolling bearings in the gearbox of giant bucket wheel excavators
The maintenance of rotating gearboxes in large machines is time-consuming, cost-intensive and very complex. Gearbox wear in large machines such as bucket wheel excavators, tunnelling machines, cement mixers or wind turbines leads to high maintenance costs and, in the worst case, to the complete failure of the machine.
As part of the "MIBRAG" research project, the team led by Prof Dr Faouzi Derbel from the Faculty of Engineering at HTWK Leipzig University of Applied Sciences has been working with Mitteldeutsche Braunkohlengesellschaft mbH (MIBRAG) since 2016 to develop wireless sensor systems that enable technical condition diagnostics for the rolling bearings of planetary gears in large machines.
Gearbox condition diagnostics now live and digital
The latest generation of MIBRAG modules developed in the project has been in use since 5 October 2021. The wireless sensor hardware transmits daily and live vibration data from inside the large gearbox of a bucket wheel excavator. This data is analysed using various mathematical methods, which calculate a forecast of the probability of failure depending on the diagnosed condition and provide recommendations for upcoming maintenance work.
The development process of the MIBRAG modules
In the past, the rolling bearings of the planetary gearboxes were serviced selectively: Vibration measurements were taken every four weeks in accordance with the DIN standard by installing vibration sensors outside the gearboxes. Due to the complexity and size of the planetary gearboxes, it was not possible to record all wear processes. From an ecological and economic point of view, there is a need for more precise and, above all, more regular technical diagnostics of the gearboxes.
In 2016, MIBRAG commissioned the team of Prof Dr Faouzi Derbel from the Faculty of Engineering at HTWK Leipzig to develop a sensor system that would be installed inside the gearboxes and enable regular digital measurement of the wear condition.
"The gearbox and bearing analyses posed a major challenge in the development of the new MIBRAG modules, as the required vibration sensors had to be installed as far inside as possible and the measured values had to be transmitted wirelessly to the outside. The compromise between sampling rate and energy requirements is just one of many exciting research topics that we have had to solve in recent years," emphasises project team member Florian Strakosch.
Data transfer through oil gears
Florian Strakosch has been involved in the "MIBRAG" research project from the very beginning and has been working on data transfer, among other things. Data transmission first had to be researched so that sensors installed inside the gearboxes could also send their measurement results through the oil by radio.
Prof Derbel and Florian Strakosch published their research findings on the propagation of electromagnetic waves in oil in the article "Investigation of Radio Propagation in Moving Gear Oils". At the 15th Multi-Conference on Systems, Signals and Devices (SSD), Strakosch and Prof Derbel received the "Best Paper Award" in 2018 and gained international recognition for their research work.
Extreme conditions
Prof Derbel's scientific team had to overcome various challenges when developing the wireless sensors. The aim was to develop sensors that could autonomously collect measurement data and send it wirelessly through oil and metal to receivers outside the gearbox, require little energy, i.e. work for a long time without changing batteries, and withstand the extreme conditions inside the gearbox.
This is because the lower part of the planetary gearbox is filled with oil to cool the gearbox, which can heat up to 95 degrees Celsius. The individual gear wheels of the planetary gearbox rotate in and out of this oil bath. The sensors to be developed, including the battery for the power supply, must therefore be able to function reliably in the hot oil and also in the air. In winter, the air in the upper area can also be sub-zero, so the sensor hardware must be able to withstand extreme temperature ranges.
5-centimetre MIBRAG modules
For the positioning of the entire sensor technology, the science team identified the centring holes in the gears, which are used to align the gear wheels during maintenance work. This limits the dimensions of the entire technology to the size of a centring screw.
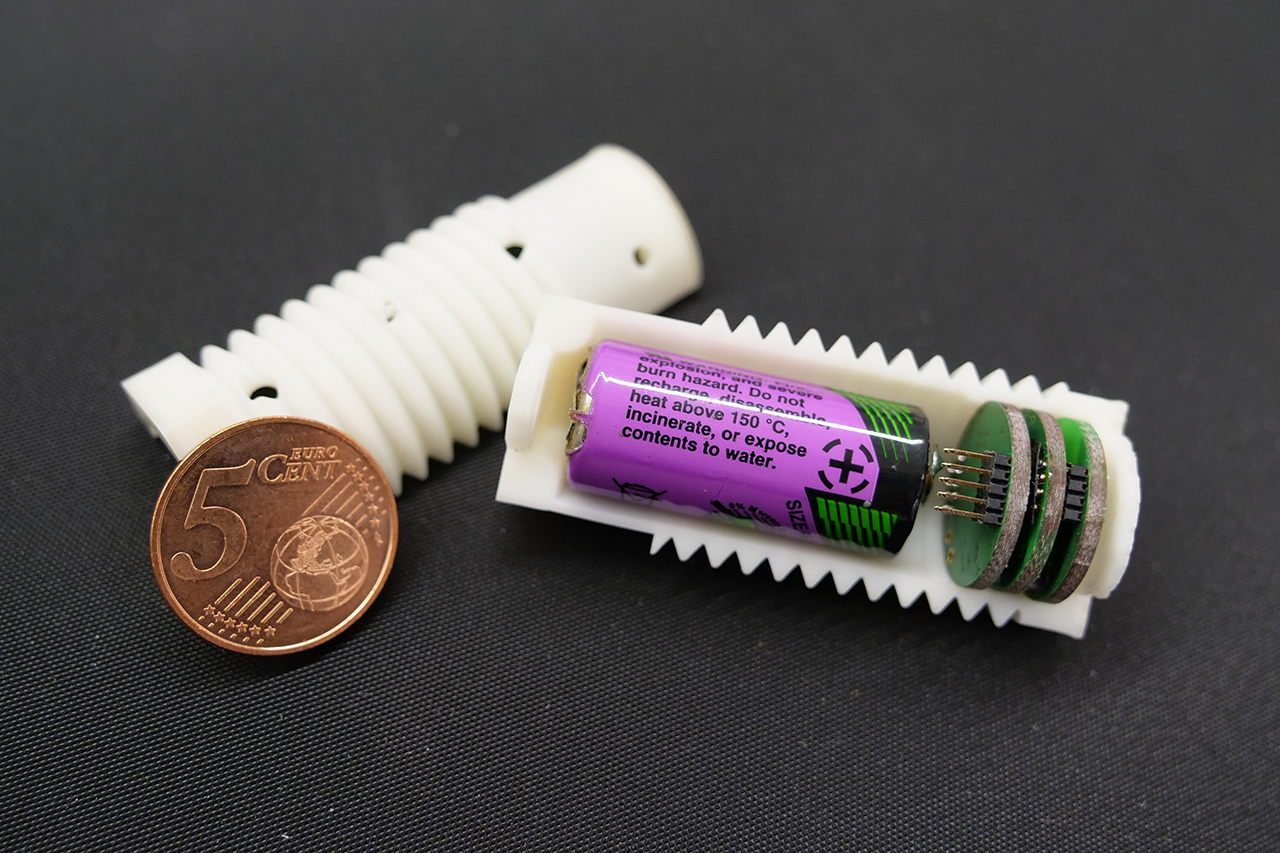
The team developed 5-centimetre MIBRAG modules consisting of multi-axis acceleration sensors, a temperature measurement, a microcontroller, a radio chip with associated antenna and a battery. All components are placed in a hollow screw, which is manufactured using a 3D printer, and enable permanent, reliable transmission diagnostics for several years.
Since 2019, the HTWK Leipzig team has been testing the MIBRAG modules in long-term use and continuously optimising individual components. The team developed its own software for data evaluation, which automatically analyses the measurement data collected by the sensor and detects faulty conditions. To do this, project team member Florian Strakosch analysed Excel lists with measured values collected in various practical tests over many years.
"The aim is to automatically read the wear on the gearbox from the measurements. To do this, I compared our data with the operating conditions of the excavator and the results of conventional gearbox diagnostics in accordance with the DIN standard. I then checked which data was relevant so that we could reduce the frequency and level of detail of the measurements to such an extent that the battery could last for several years," explains project team member Florian Strakosch.
On 5 October 2021, the latest generation of wireless sensor hardware was successfully put into operation in the planetary gearbox of the bucket wheel excavator 1553 in the Profen opencast mine.
Possible applications
The MIBRAG modules were developed for diagnosing the condition of oil-cooled planetary gearboxes in large-scale open-cast mining equipment, but the range of applications for the wireless sensor modules can be extended to all planetary gearboxes and can be used to diagnose gearbox wear in wind turbines, cement factories and giant tunnel boring machines, for example.