Students of the "Powder Metallurgy and Sintered Materials" module on an excursion to Schunk Sintermetalltechnik in Thale.
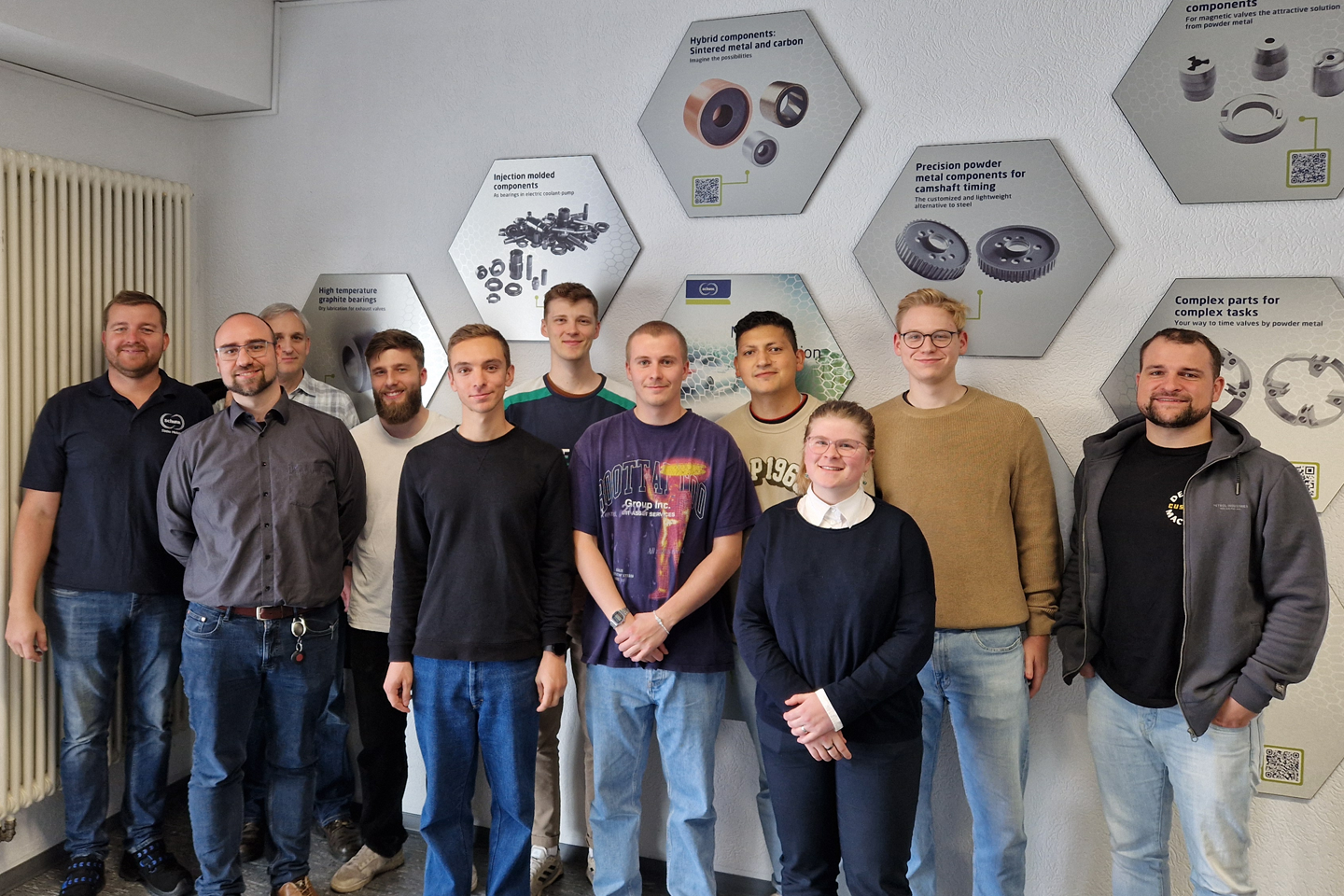
On 18 October 2024, students on the "Powder Metallurgy and Sintered Materials" module in the Faculty of Engineering were able to take part in an exciting excursion to the company Schunk Sintermetalltechnik in Thale took part. In the town of Thale, which can look back on a three-century-old tradition of metal processing, components have been manufactured from metal powder for more than 70 years. Schunk Sintermetalltechnik in Thale currently processes more than 20 tonnes of metal powder per day into complex components.
The almost fully automated production process includes pressing the metal powder into green compacts, machining the green compacts using various cutting processes, sintering in a continuous furnace at more than 1100 °C, mechanical post-compaction - calibration - to create a highly resilient component, as well as finishing and fine machining. The extremely high number of components that can be produced cost-effectively using sintered metal technology is particularly impressive. A new green compact is produced in each powder press approximately every 4-6 seconds. Various production lines each produce more than 10,000 components per day.
In the first part of the tour, the students were able to take a detailed look at this complex manufacturing process, from the metal powder delivery to the finished component for so-called "camshaft phasers", thus deepening their knowledge acquired in the "Powder metallurgy and sintered materials" module. With the high productivity of sintered metal technology, Schunk Sintermetalltechnik Thale supplies numerous companies in the automotive industry. Customers include Audi, BMW, Daimler, Ford, GM with Opel and Vauxhall as well as MAN, Porsche, PSA, Seat, Skoda, Volkswagen and Volvo.

The second part of the tour included a visit to the production line using MIM (metal injection moulding) technology. In this process, metal powder is combined with plastic powder to form a "feedstock", which is moulded into complex components using plastic injection moulding machines. After moulding, the plastic is removed from the raw parts and they are sintered in a vacuum at temperatures of more than 1200 °C to create high-density and highly resilient components. Nothing of the plastic remains. Using MIM technology, geometrically complex and highly stressed components for civil aviation engines are mass-produced in Thale for Rolls-Royce Aerospace. Schunk Sintermetalltechnik Thale is now the largest MIM manufacturer in Germany.
We would like to thank the team at Schunk Sintermetalltechnik Thale, in particular Mario Festerling (Team Leader Project Management), Marcus Trapp (Team Leader Process Management) and Thomas Wilke (Head of Maintenance), who organised and made this fantastic excursion possible for us.